Industry 4.0 with cognitive manufacturing
- Dhaval Patel
- Nov 12, 2021
- 3 min read
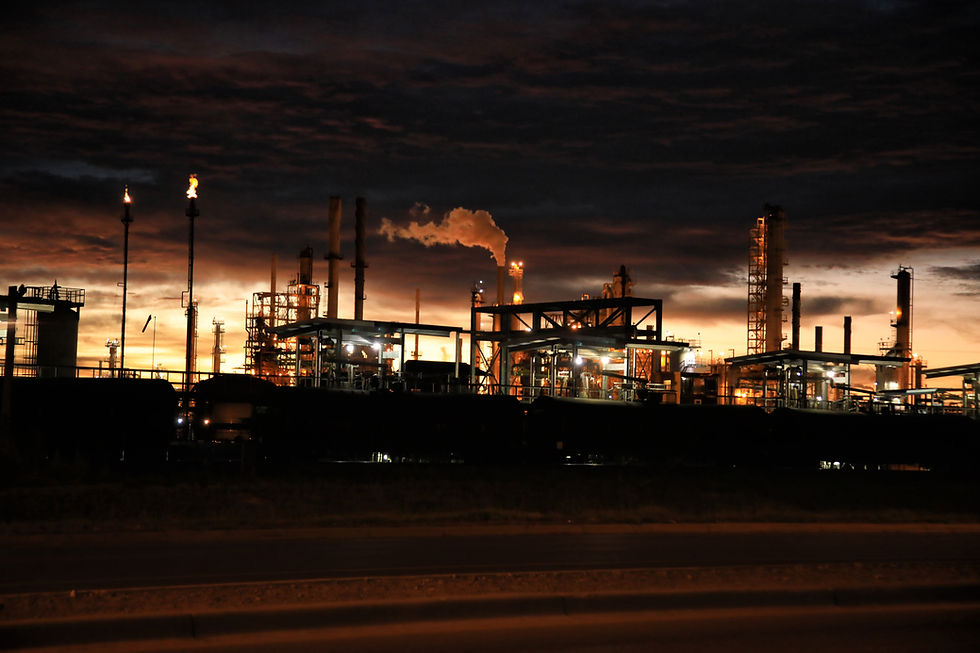
What Is Cognitive Manufacturing?
Cognitive manufacturing utilizes cognitive computing, the Industrial IoT, and advanced analytics to advance manufacturing forms in manners that were not already possible. It enables organizations to improve key business metrics, for example, efficiency, item dependability, quality, security and yield, while reducing downtime and lowering costs.
What It Is and Why It Matters
Cognitive technologies look deeply into a manufacturing process and business environment to derive information that has tangible value for a manufacturer. Cognitive manufacturing leverages cognitive computing, the Industrial IoT, and advanced analytics to digitize, understand and optimize manufacturing processes in ways that were not previously possible.
Cognitive manufacturing is powerful because it combines sensor-based information with machine learning and other artificial intelligence capabilities to find patterns in structured and unstructured data from plant, enterprise and industry systems. It pulls relevant information together in real time and applies analytics to yield unprecedented levels of understanding and insights about the manufacturing process.
The average factory produces more than a terabyte’s worth of information every day, but 99 percent of this data isn’t being analyzed. The result is a closed loop — a manufacturing box that contains information but can’t effectively leverage it to streamline production. As the shift to Industry 4.0 picks up speed, enterprises are looking for ways to empower process visualization and lay the foundation for cognitive manufacturing.
Key Issues Cognitive Technologies Address for Manufacturers
Manufacturers can use cognitive technologies to solve fundamental business challenges, find new value in their manufacturing data, improve quality and enhance knowledge management in their organizations.
Solving business challenges: Cognitive manufacturing enables associations to improve crucial business measurements, for example, profitability, item dependability, quality, security, and yield while reducing downtime and lowering costs. Applications can be anything but difficult to utilize and produce quick advantages. For instance, a field expert sent to fix a machine can just submit manifestations into an intellectual motor that will at that point dissect the side effects and recommend a lot of fix choices positioned arranged by likelihood of achievement. The methodology improves the first run through a fix rate, which improves efficiency and diminishes costs.
Creating new value from manufacturing data: Cognitive advances look profoundly into an assembling procedure and business condition to infer data that has a substantial incentive for a manufacturer. The process considers new information sources just as unstructured information and applies advanced analytical models to discover noteworthy connections that weren't uncovered in the information previously. By utilizing cognitive advancements, predictive maintenance activities—previously reliant on historical data—can be enriched with information found in technician logs, maintenance records, emails, and other sources. Product inspections can be performed by cognitive visual assessment frameworks that gain from pictures of made items to distinguish abandons and decide whether the deformities are attached to quality issues. Organizations that utilization these kinds of procedures can improve plant tasks and execution and diminish costs also.
Improving product quality: Successful manufacturers are always striving to build the best-quality products. In a recent survey of electronics manufacturers, for example, IBM found that two-thirds (66%) of company executives consider minimizing defects and achieving a higher rate of accuracy in production to be key performance indicators for their facilities. Cognitive manufacturing enables companies to put a laser-like focus on quality throughout the life cycle of a product’s development—from design through manufacturing and even after distribution when companies must ensure product quality through warranty and support programs. The approach improves yield, reduces overall warranty costs, and helps ensure customer satisfaction for the lifetime of a product.
Enhancing knowledge management: Cognitive manufacturing is tied in with exploiting data, information from differing sources—hardware sensors, yet additionally logs, manuals, worker biometric monitors or the environment. The methodology joins these kinds of sources and information into the logical procedure to make a proficient framework that is consistently learning. It can make shrewd operational suggestions dependent on a far-reaching comprehension of manufacturing conditions.
Four Compelling Applications for Cognitive Manufacturing
Asset Performance Management – Improving reliability and performance of equipment and assets through better visibility, predictability and operations
Process and Quality Improvement – Optimizing yield and productivity of manufacturing operations, from design through warranty support
Resource Optimization—Improving safety of workers and optimizing energy efficiency and facility productivity while reducing costs
Supply Chain Optimization—Improving visibility and insights to build a dynamic supply chain that accelerates innovation
Cognitive manufacturing enables companies to put a laser-like focus on quality throughout the life cycle of a product’s development – from design through production and warranty support.
Reference:
Commentaires