The Resilient Supply Chain
- Dhaval Patel
- Nov 12, 2021
- 3 min read
Supply chains today are complex and global, and for many are regularly disrupted, often opaque and increasingly regulated. Coupled with the megatrends of accelerating urbanization, resource scarcity and the breath-taking pace of technology proliferation, supply chains continue to rapidly evolve and transform. Yet, the majority of companies do not regularly assess the resilience of their supply chain:
· 90%* do not know if key suppliers have business continuity plans
· 75%* experience at least one major supply chain disruption a year
· 42%* experience a major disruption below tier 1
Increasing resilience and preventing the cost and revenue impacts of these disruptions affects the entire spectrum of supply chain risks – product, supplier, network and environmental – as well as demand chain and back office technology. It requires a new approach – adopting a scenario focus to identify and manage the challenges and opportunities that encompass external events and internal lapses.
How to build a resilient supply chain?
A resilient supply chain balances risk and costs to prevent or recover quickly from a multitude of dynamic and simultaneous risk-related disruptions. Resilient supply chains are characterized by four pillars.
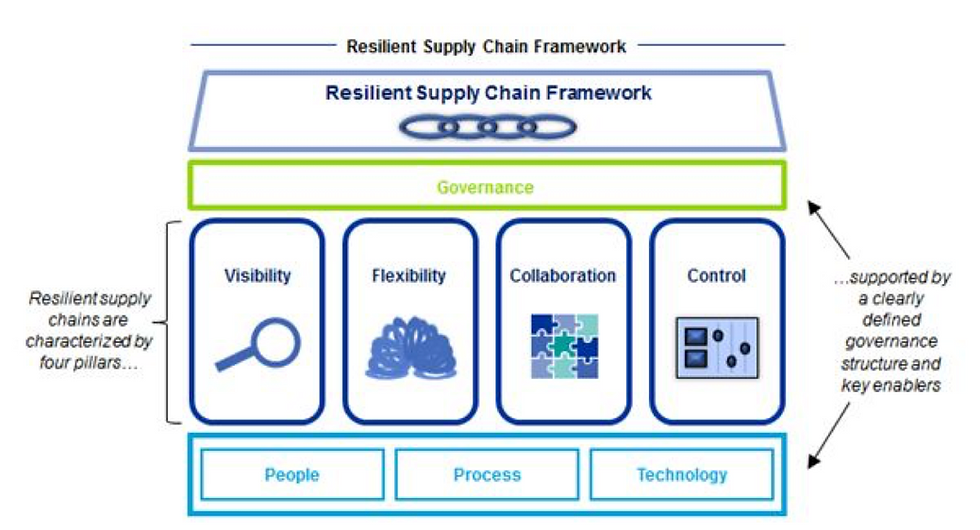
Visibility The ability to track and monitor supply chain events and patterns, enabling proactive actions:
· Monitoring of supplier performance and compliance
· Ability to monitor flow of material from tier three suppliers to end-users
· Line of sight into end-user consumption and usage patterns
Flexibility The ability to quickly adapt to disruptions without significantly increasing operational costs:
· Identification of alternate suppliers that can manufacture core products in the event of a disruption
· Ability of a single manufacturing line to produce multiple products
· Ability to re-route materials to meet changing demands
To achieve effective visiblity and flexiblity, objective and comparable metrics were required. Cisco created an index to assess time-to-recover for all capabilities, including a supplier, product or particular supply chain design. This index comprises multiple categories: component (30%), supplier (20%), manufacturing (30%) and test equipment (20%). These scores are reported semiannually to senior management by the general managers. This monitoring system helps ensure that product designers think about resiliency as a product attribute and that operations executives are cognizant of suppliers’ resiliency gaps and address them.
Collaboration The ability to develop symbiotic and trust-based relationships with supply chain partners and other key strategic networks:
· Collaborative planning with suppliers and customers
· Collaborative design in products – incorporating customer demands and supplier capabilities
· Access to end-to-end supply chain inventory data and supplier capacity constraints
Control The ability to implement policies and execute processes to prevent disruptions:
· Ability to develop products with appropriate levels of quality and safety
· Ability to protect end-to-end product flow (e.g. tampering, theft, counterfeiting)
· Adequate regulatory, legal and social compliance policies and controls
For an organisation to have a robust and resilient supply chain, the above four elements must be present. This can be difficult to achieve but it is possible from small to medium food and beverage producers to large pharmaceutical multi-nationals. The key is to successfully select a portfolio of resilience strategies that effectively and efficiently reduce specific vulnerabilities in the relevant supply chain.
In building and maintaining resilience, organisations must also develop and implement effective governance structures and key enablers. A key principle for effective governance is selecting an individual or a defined group of individuals as the accountable owner for supply chain resilience and risk issues.
Examples of enablers of good governance include:
· Processes - policies and level of control and monitoring
· People - culture, roles and responsibilities and awareness
· IT - risk databases and analytics, modelling and simulation and reporting dashboard
Talking about Cisco, Cisco engineers assessed critical value chain partners to (1) identify key supply chain nodes where a disruption would have a particularly high impact, (2) evaluate risks based on likelihood and impact, using simulations, (3) map critical components to the sites that supply them and (4) evaluate and audit business continuity planning procedures for supply chain nodes. This monitoring & control action, combined with event-scenario planning and simulation, which helps Cisco determine what corrective actions should be implemented first.
The rewards for building a resilient organization are substantial. The “hardened” enterprise will be able to not only withstand all manner of disruption but also increase its competitiveness. Unforeseen disruptions can create shortages that are not dissimilar to the demand spikes caused by supply/demand imbalances; resilient enterprises can thus react to changing market demand ahead of their competitors.
References:
Comentarios